Due to its special structure and mixing capacity, the three-screw extruder has shown unique advantages in some applications that require a high degree of mixing uniformity. The following are several application cases of three-screw extruders
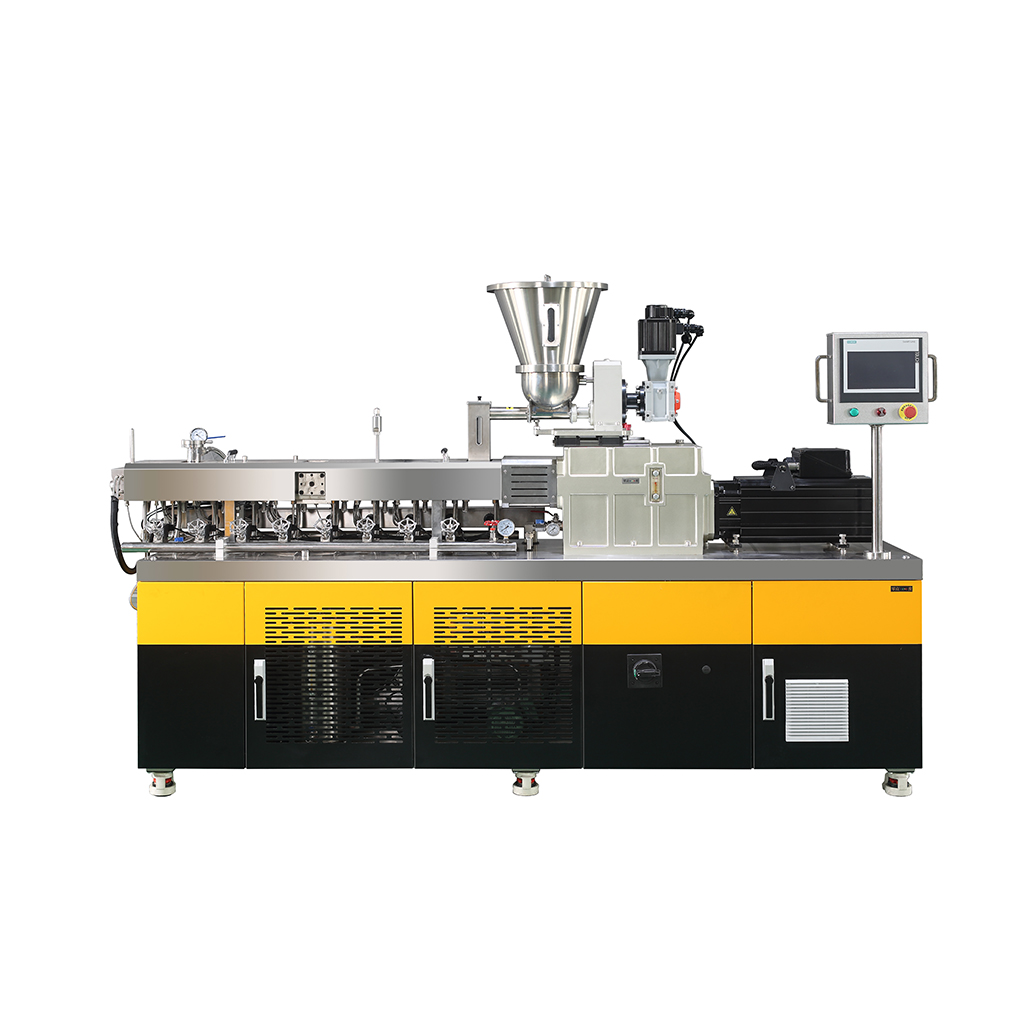
- High temperature material processing
application case: Processing polyetheretherketone (PEEK) and polyimide (PI)
process overview: - Raw material preparation: Add PEEK or PI granules and additives (such as fillers, lubricants) into the hopper.
- Heating and melting: The raw materials are melted by passing through the heating zone of the three-screw extruder.
- Mixing and plasticizing: The molten materials are mixed and plasticized under the special design of three screws.
- Extrusion: Plasticized material is extruded through a die into the desired shape.
- Cooling and solidification: The extruded product is solidified by cooling water trough or air cooling.
Key equipment: three-screw extruder, heater, mold, cooling system.
Technical points: screw design, heating temperature control, and mold accuracy.
- Biodegradable plastics processing and production process of
biodegradable plastics : - Raw material preparation: Add bio-based polymers (such as PLA, PBS) and additives (such as plasticizers, antioxidants) into the hopper.
- Heating and mixing: The raw materials are melted and mixed evenly through the heating zone of the three-screw extruder.
- Plasticization: The molten material is further plasticized under the special design of the three-screw.
- Extrusion molding: The plasticized material is extruded into the desired shape through a die.
5. Cooling molding: The extruded product is solidified by cooling water tank or air cooling.
Key equipment: three-screw extruder, heater, mold, cooling system.
Technical points: special design of screw, control of heating temperature, and design of mold.
- High-performance composite materials production process of
carbon fiber reinforced nylon composite materials : - Raw material preparation: Add nylon resin and carbon fiber into the hopper.
- Heating and mixing: The raw materials are melted and mixed evenly through the heating zone of the three-screw extruder.
- Mixing and plasticizing: The molten material is further plasticized under the special design of the three-screw.
- Extrusion: Plasticized material is extruded through a die into the desired shape.
- Cooling and solidification: The extruded product is solidified by cooling water trough or air cooling.
Key equipment: three-screw extruder, heater, mold, cooling system.
Technical points: special design of screw, control of heating temperature, and design of mold.
- High-end masterbatch preparation
application case: Production
process of high-concentration masterbatch: - Raw material preparation: Add base resin and high-concentration pigment into the hopper.
- Heating and mixing: The raw materials are melted and mixed evenly through the heating zone of the three-screw extruder.
- Mixing and plasticizing: The molten material is further plasticized under the special design of the three-screw.
- Extrusion: Plasticized material is extruded through a die into the desired shape.
- Cooling and solidification: The extruded product is solidified by cooling water trough or air cooling.
Key equipment: three-screw extruder, heater, mold, cooling system.
Technical points: special design of screw, control of heating temperature, and design of mold.
- Polymer modification
application case: Production
process of modified polycarbonate (PC): - Raw material preparation: Add polycarbonate and modifiers (such as flame retardants, antistatic agents) into the hopper.
- Heating and mixing: The raw materials are melted and mixed evenly through the heating zone of the three-screw extruder.
- Mixing and plasticizing: The molten material is further plasticized under the special design of the three-screw.
- Extrusion: Plasticized material is extruded through a die into the desired shape.
- Cooling and solidification: The extruded product is solidified by cooling water trough or air cooling.
Key equipment: three-screw extruder, heater, mold, cooling system.
Technical points: special design of screw, control of heating temperature, and design of mold.
The three-screw extruder can achieve more efficient mixing in the above applications, especially for applications that require high dispersion and complex mixing processes. Its unique geometric structure and mixing capacity enable the three-screw extruder to achieve good mixing effects within a shorter screw length, which is crucial to improving production efficiency and product quality.